This could cover a multitude of things ranging from a trip to Halfords to an Auto-jumble or Loft’s garage.
But this was different – I needed a bracket to mount the recently acquired Klaxon on the bulkhead of the Amilcar.
So I advertised in the VSCC bulletin in the “Wanted” column, or so I thought. Instead, it went into the “For Sale” column and that’s how I found out that at least 4 or 5 others also wanted a bracket, so I became the elected procurer.
Fortunately one of our number managed to find a bracket which he lent me and I duly sent it off to Harling Foundries in Hastings… http://www.harling.f9.co.uk/
Rather than have them send the brackets to me I decided to go to collect them myself, little realising what a treat was in store.
When I asked for directions Lloyd said “…you’ll see the silo first”; now I acquaint silos with farming so I was in for a bit of a shock when I found the entrance on an industrial estate which seemed like an early 20th century version of a Dickensian workhouse.
The silo was of course where they stored all the sand with which they made the moulds for the castings. Outside there was a skip full of what looked like old bricks but were the cast offs (sorry).
Inside there were about 5 people plus Lloyd, who gave me a conducted tour.
As we went in there was a batch of Healey 3000 cylinder heads waiting for machining. Whilst Lloyd was cleaning the Klaxon brackets up after heat-treatment which apparently leaves them a blackish tinge which rubs off easily enough, I had a look around.
There on the floor were a batch of 10 of what looked like motorcycle heads – I wasn’t far wrong, but they were for Messerschmitts
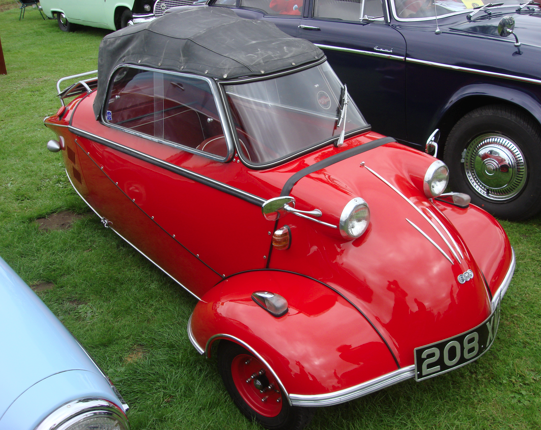
Next to that were a lot of wooden boxes for the sand for the moulds and they had someone’s name on the them and after it, the name of the car…
250 GTO
Apparently the owner likes to use his Ferrari but rather than risk damaging the original head he was having a batch made which he could use for racing…and No, his name wasn’t Chris Evans.
The downstairs of the Foundry was where all the moulds were made and cast and then sent away to be machined. Part of the upstairs was where they stocked the six or so different types of alloys which they use.
The other upstairs part was the office or inner sanctum; there was a white board there with such magic names as Crossthwaite and Gardiner on it www.crosthwaiteandgardiner.com/ - they are the company who have been building or rebuilding Auto Unions for Audi.
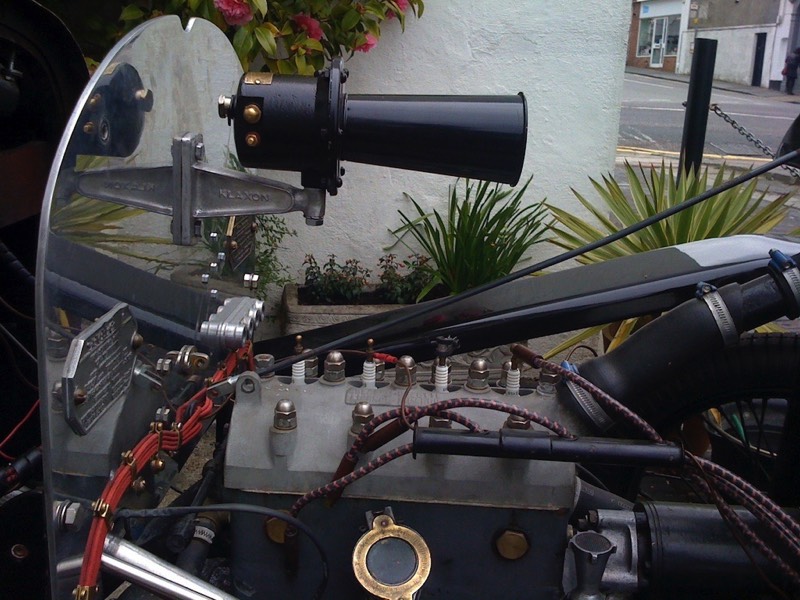